Exactly how to Determine What is Porosity in Welding and Improve Your Method
Exactly how to Determine What is Porosity in Welding and Improve Your Method
Blog Article
Comprehending Porosity in Welding: Discovering Causes, Effects, and Prevention Methods
Porosity in welding is a consistent obstacle that can dramatically influence the top quality and honesty of welds. As professionals in the welding sector are cognizant, comprehending the causes, impacts, and prevention methods associated with porosity is vital for attaining robust and reliable welds. By diving right into the source of porosity, examining its destructive results on weld top quality, and exploring efficient prevention methods, welders can improve their understanding and skills to generate high-grade welds constantly. The intricate interaction of aspects adding to porosity needs a thorough understanding and an aggressive technique to guarantee successful welding end results.
Usual Root Causes Of Porosity
Contamination, in the kind of dust, oil, or rust on the welding surface area, develops gas pockets when warmed, leading to porosity in the weld. Incorrect securing happens when the securing gas, frequently utilized in procedures like MIG and TIG welding, is not able to totally safeguard the liquified weld swimming pool from responding with the surrounding air, resulting in gas entrapment and succeeding porosity. Additionally, poor gas coverage, often due to wrong flow prices or nozzle positioning, can leave parts of the weld vulnerable, allowing porosity to create.
Results on Weld Quality
The visibility of porosity in a weld can substantially jeopardize the general quality and stability of the welded joint. Porosity within a weld develops voids or tooth cavities that deteriorate the structure, making it much more at risk to splitting, corrosion, and mechanical failing. These gaps function as tension concentrators, reducing the load-bearing capacity of the weld and increasing the probability of premature failure under applied stress. Additionally, porosity can additionally serve as potential websites for hydrogen entrapment, further intensifying the deterioration of the weld's mechanical properties.
In addition, porosity can prevent the efficiency of non-destructive screening (NDT) techniques, making it testing to find other flaws or gaps within the weld. This can bring about substantial safety and security problems, specifically in vital applications where the structural integrity of the welded parts is extremely important.

Prevention Techniques Review
Provided the damaging effect of porosity on weld high quality, efficient prevention methods are critical to maintaining the architectural honesty of bonded joints. Furthermore, choosing the appropriate welding a knockout post criteria, such as voltage, existing, and travel speed, can aid decrease the threat of porosity formation. By including these prevention techniques into welding practices, the event of porosity can be dramatically minimized, leading to more powerful and more dependable welded joints.
Importance of Correct Protecting
Appropriate securing in welding plays an essential duty in protecting against climatic contamination and guaranteeing the integrity of bonded joints. Securing gases, such as argon, helium, or a combination of both, are commonly made use of to secure the weld pool from responding with aspects airborne like oxygen and nitrogen. When these reactive aspects come into call with the warm weld pool, they can trigger porosity, bring about weak welds with minimized mechanical homes.
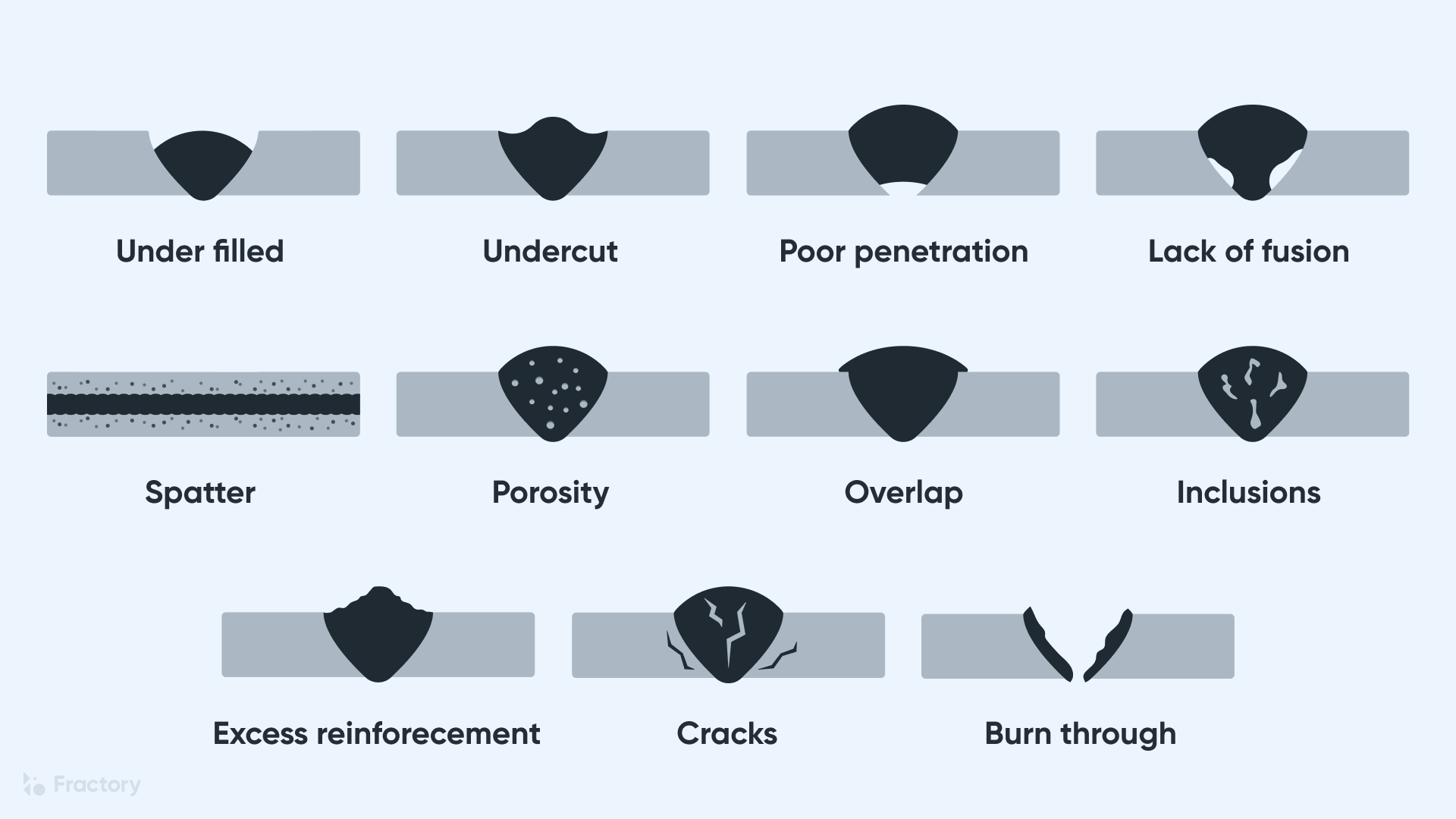
Inadequate protecting can result in numerous defects like porosity, spatter, and oxidation, endangering the structural honesty of the welded joint. Adhering to go now appropriate securing practices is necessary to produce high-quality welds with very little defects and guarantee the long life and reliability of the welded elements.
Monitoring and Control Approaches
Exactly how can welders successfully check and control the welding process to ensure ideal outcomes and avoid problems like porosity? By constantly checking these variables, welders can identify discrepancies from the suitable conditions and make immediate modifications to prevent porosity development.

Furthermore, applying correct training programs for welders is crucial for keeping an eye on and controlling the welding procedure effectively. What is Porosity. Informing welders on the importance of preserving consistent parameters, such as appropriate gas shielding and take a trip rate, can aid protect against porosity problems. Routine analyses and qualifications can additionally ensure that welders excel in monitoring and regulating welding processes
Furthermore, making use of automated welding systems can boost surveillance and control abilities. These systems can exactly manage welding parameters, minimizing the probability of human mistake and ensuring constant weld top quality. By incorporating advanced monitoring innovations, training programs, and automated systems, welders can successfully monitor and regulate the welding procedure to minimize porosity flaws and accomplish top notch welds.
Conclusion
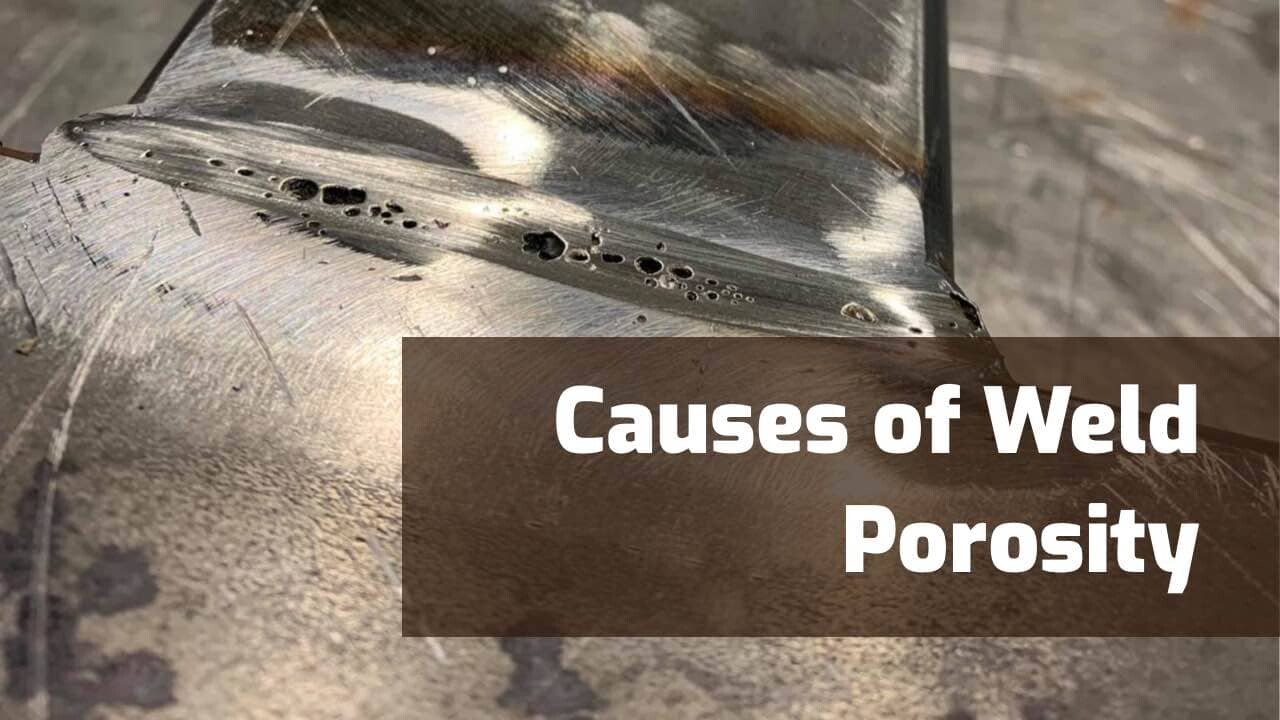
Report this page